Unlock Excellence with Expert CNC & Lathe Machining at Best Prices
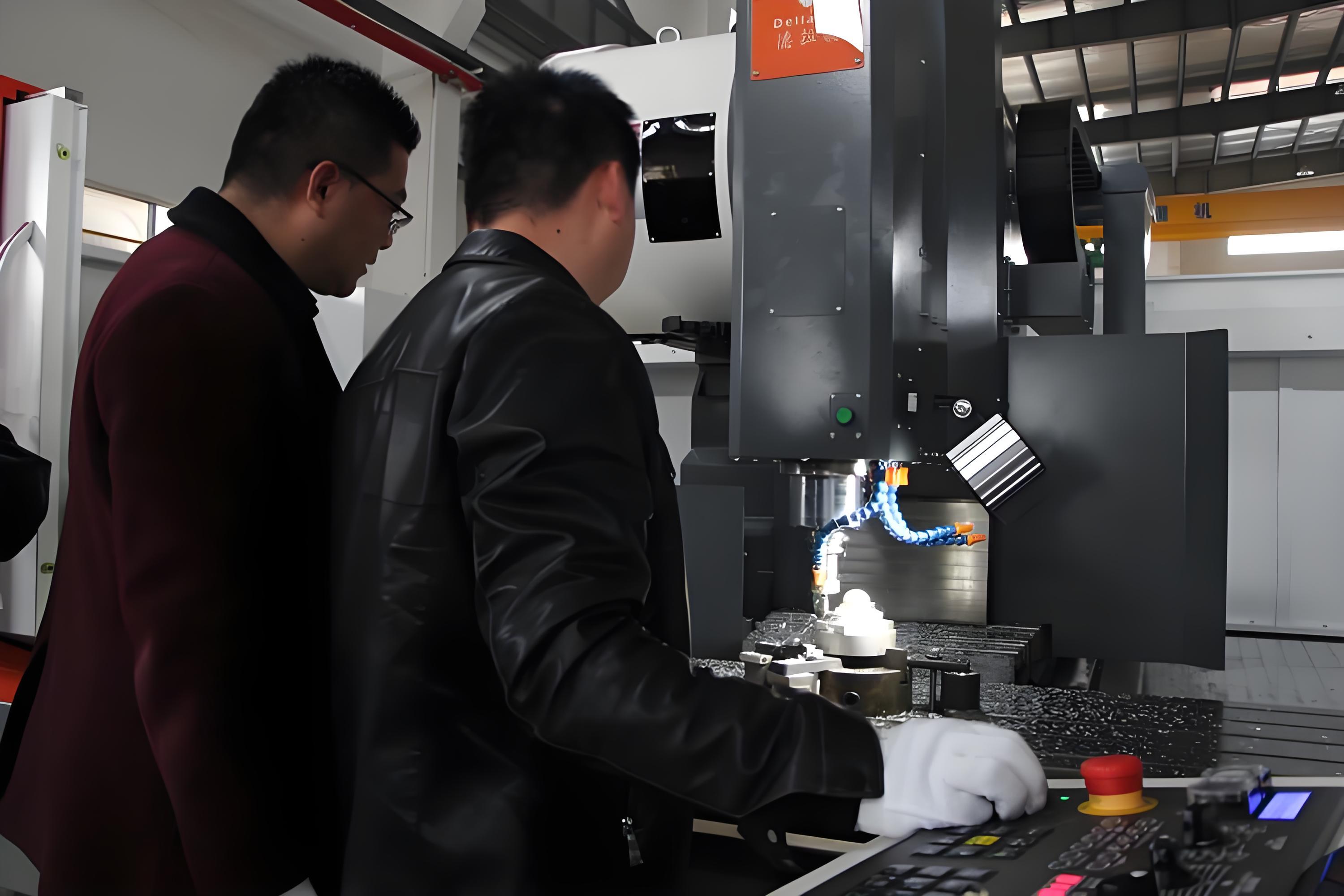
1、Introduction
Expert CNC and lathe machining are crucial in the modern manufacturing industry. This article explores the benefits and features of these processes, highlighting why they are the go-to choice for high-quality and cost-effective production.
In today's highly competitive manufacturing landscape, precision and efficiency are of utmost importance. Computer Numerical Control (CNC) machining and lathe machining play a vital role in meeting these demands.
CNC machining, as the name suggests, is a process controlled by computers. It utilizes advanced software and programming to guide machines in performing various operations with remarkable accuracy. CNC machines can handle a wide range of materials, from metals like steel and aluminum to plastics and composites.
Lathe machining, on the other hand, is focused on rotating the workpiece while cutting tools are applied to shape it. This method is particularly useful for creating cylindrical parts and is widely used in industries such as automotive, aerospace, and medical.
One of the key advantages of both CNC and lathe machining is their ability to achieve high precision. With micron-level accuracy, these processes can produce parts that meet the strictest quality standards. This is essential in industries like aerospace and medical equipment manufacturing, where even the slightest deviation can have serious consequences.
Consistency is another major benefit. Unlike traditional manual machining methods, CNC and lathe machining ensure that each part produced is identical in size and shape. This is crucial for mass production, as it reduces the likelihood of errors and rework.
Automation is a significant feature of these processes. CNC and lathe machines can operate continuously with minimal human intervention, increasing production efficiency and reducing labor costs. Operators only need to set up the machine, load the materials, and monitor the process.
Flexibility is also a hallmark of CNC and lathe machining. The programming can be easily adjusted to accommodate different part designs and specifications, making it suitable for both small batch production and large-scale manufacturing.
In addition to these benefits, CNC and lathe machining offer safety advantages. As most of the operations are automated, workers are less exposed to dangerous machinery, reducing the risk of accidents.
To better understand these processes, let's take a look at some of the common applications. In the aerospace industry, CNC and lathe machining are used to manufacture complex components such as engine parts and structural elements. The high precision and consistency required in aerospace manufacturing make these processes ideal.
In the automotive sector, they are employed to produce engine components, transmission parts, and body panels. The ability to handle large volumes of production while maintaining quality is a major advantage.
The medical field also relies on CNC and lathe machining for producing surgical instruments, implants, and other precision medical devices. The strict quality standards and need for accuracy make these processes essential.
In conclusion, expert CNC and lathe machining offer a combination of precision, efficiency, consistency, flexibility, and safety that makes them indispensable in the modern manufacturing industry. Whether it's for aerospace, automotive, medical, or other industries, these processes are the go-to choice for high-quality and cost-effective production.
2、Benefits of Expert CNC and Lathe Machining
2.1 Precision and Accuracy
CNC machining offers tolerances down to ±0.017 mm, ensuring highly accurate parts. Lathe machining also provides precise results, making it ideal for complex designs.
The precision and accuracy of expert CNC and lathe machining are crucial in various industries. With CNC machining, tolerances can be as low as ±0.017 mm. This level of precision ensures that the parts produced are highly accurate and meet the strictest quality standards. For example, in the aerospace industry, where even the slightest deviation can have serious consequences, such precision is essential. Lathe machining also offers precise results. It is particularly useful for creating cylindrical parts and is widely used in industries like automotive, aerospace, and medical. The ability to achieve high precision in both CNC and lathe machining makes them ideal for complex designs that require exact dimensions and shapes.
2.2 Versatility
Capable of handling a wide range of materials and part geometries, from simple to highly complex components.
Expert CNC and lathe machining are highly versatile. They can handle a wide range of materials, including metals like steel, aluminum, copper, titanium, and various plastics and composites. This versatility allows manufacturers to produce parts for different applications and industries. Moreover, these processes can handle part geometries ranging from simple to highly complex. Whether it's a basic cylindrical shape or a complex three-dimensional structure with intricate details, CNC and lathe machining can handle it. For instance, in the medical field, surgical instruments and implants often require complex geometries that can be achieved through these machining processes.
2.3 Efficiency
Saves time with multiple operations performed simultaneously and quick turnaround times.
Efficiency is another significant benefit of expert CNC and lathe machining. These processes can perform multiple operations simultaneously. For example, a CNC machine can drill, mill, and contour in a single setup, saving time and reducing the need for multiple machines. This not only increases productivity but also reduces labor costs. Additionally, quick turnaround times are possible due to the automation and high-speed capabilities of these machines. Operators can set up the machine, load the materials, and monitor the process while the machine works continuously. In industries where time is of the essence, such as automotive and electronics, this efficiency is highly valuable.
2.4 Cost-Effective
Despite high precision, can offer competitive prices, especially for large volume orders.
Despite their high precision and advanced capabilities, expert CNC and lathe machining can be cost-effective. While the initial investment in these machines may be significant, the long-term benefits outweigh the costs. For large volume orders, the cost per part can be competitive due to the efficiency and productivity of these processes. Moreover, the ability to produce parts with high accuracy reduces the likelihood of errors and rework, saving time and money. In addition, the versatility of these machines allows manufacturers to produce a wide range of parts, reducing the need for multiple specialized machines. This further contributes to cost savings.
3、High-Quality CNC and Lathe Machining Processes
3.1 CNC Machining
1. Milling, turning, and surface treatment.
CNC machining involves various processes such as milling, turning, and surface treatment. Milling is a process where a rotating cutting tool removes material from a workpiece to create complex shapes and features. Turning, on the other hand, is the process of rotating the workpiece while a cutting tool is applied to shape it. Surface treatment is also an important aspect of CNC machining as it can enhance the appearance and durability of the final product.
2. Advanced equipment like CNC centers, four-axis and five-axis machines.
Advanced equipment plays a crucial role in high-quality CNC machining. CNC centers are equipped with multiple tools and can perform a variety of operations simultaneously. Four-axis and five-axis machines offer even greater flexibility and precision, allowing for complex geometries to be machined with ease. These machines can handle a wide range of materials and are capable of achieving extremely tight tolerances.
3.2 Lathe Machining
3. Swiss-type lathes for high-precision turning.
Swiss-type lathes are known for their high-precision turning capabilities. They are designed to handle small, complex parts with great accuracy. The precision turning offered by Swiss-type lathes is essential in industries such as medical and electronics, where even the slightest deviation can have a significant impact on the functionality of the final product.
4. Combined turning-milling services.
Combined turning-milling services provide a comprehensive solution for manufacturing complex parts. By integrating turning and milling operations, manufacturers can achieve greater efficiency and accuracy. This approach is particularly useful for parts that require both cylindrical and flat surfaces or features that cannot be achieved with a single machining process.
4、CNC Machining Services at Competitive Prices
4.1 Service Providers
5. Leading CNC machining companies with state-of-the-art equipment and experienced teams.
In the field of CNC machining, there are several leading companies that stand out for their exceptional capabilities. These companies are equipped with the latest in CNC technology, including advanced machines and software. Their teams of experienced machinists bring years of expertise to every project, ensuring high-quality results. For example, companies like Avanti Engineering, Inc. and Technox Machine & Mfg Co have been leaders in the CNC machining industry for many years. They utilize state-of-the-art CNC machining centers with the latest technology to produce intricate and accurate parts with tight tolerances. Their skilled programmers and machinists can handle both small and large production runs, delivering exceptional results every time.
6. ISO certified factories for quality assurance.
ISO certification is a mark of quality and reliability in the CNC machining industry. Factories that are ISO certified adhere to strict quality management systems, ensuring that every part produced meets the highest standards. For instance, Valk Industries, Inc. is ISO 9001:2008 certified, demonstrating their commitment to quality. This certification shows that they have implemented processes and procedures to ensure consistent quality, from the initial design phase to the final product. It gives customers confidence that the parts they receive will be of the highest quality and meet their exact specifications.
4.2 Cost Savings
7. Efficient production processes reduce overall costs.
Efficient production processes are essential for reducing costs in CNC machining. By optimizing the machining process, companies can save time and resources, ultimately reducing the overall cost of production. For example, using advanced software and programming techniques can minimize waste and maximize productivity. Additionally, techniques like high-speed precision machining and five-axis CNC machining can reduce production time and increase efficiency. As mentioned in the "efficient production" and "high efficient production" sections, these methods can lead to significant cost savings. Companies can also implement lean manufacturing principles to eliminate waste and improve efficiency. This includes streamlining workflows, reducing setup times, and optimizing machine utilization.
8. In-house secondary services save time and money.
Many CNC machining companies offer in-house secondary services, which can save time and money for customers. These services may include surface treatment, heat treatment, and assembly. By providing these services in-house, companies can reduce lead times and eliminate the need for outsourcing. For example, Share Machine Inc offers a wide range of services, including five-axis machining, high-speed precision machining, and reverse engineering. They also provide in-house electrical motor rebuilding services through Share Motor Services. This comprehensive approach allows customers to get all their machining needs met in one place, saving time and money. Additionally, companies like Blanda Inc. offer a variety of services, including CNC milling and turning, wire EDM, waterjet cutting, and precision grinding. Their ability to handle multiple processes in-house gives them an edge in providing cost-effective solutions to customers.
5、Conclusion
Expert CNC and lathe machining truly offer an unbeatable combination of advantages. Whether for small prototypes or large-scale production runs, these processes are essential for obtaining high-quality custom machined parts. When choosing a provider for your next project, look for one with a reputation for reliability. A reliable provider will have state-of-the-art equipment, such as advanced CNC centers and four-axis or five-axis machines for CNC machining, and Swiss-type lathes for high-precision turning in lathe machining. They will also have an experienced team that can handle a wide range of materials and part geometries.
Moreover, a reliable provider will likely be ISO certified, ensuring quality assurance. This means that every part produced will meet the highest standards, giving you confidence in the final product. In addition to quality, cost-effectiveness is another important consideration. Efficient production processes, such as performing multiple operations simultaneously and optimizing machining techniques, can reduce overall costs. In-house secondary services can also save time and money by eliminating the need for outsourcing.
In conclusion, choosing a reliable expert in CNC and lathe machining unlocks the full potential of these processes. You can expect precision, versatility, efficiency, cost-effectiveness, flexibility, and safety. Whether your project is in aerospace, automotive, medical, or any other industry, these machining processes are the go-to choice for high-quality production.
Rapidefficient website: https://rapidefficient.com
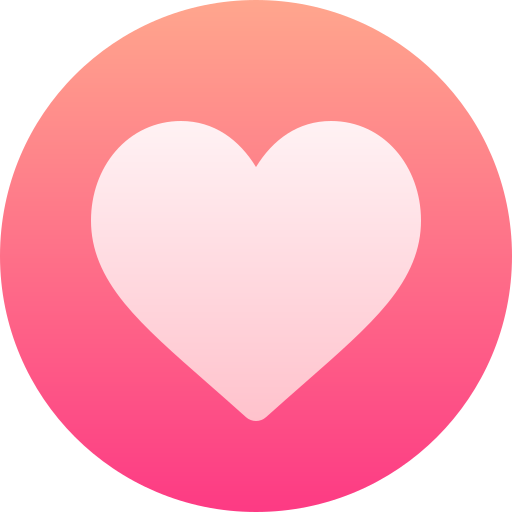
- Art
- Causes
- Crafts
- Dance
- Drinks
- Film
- Fitness
- Food
- ເກມ
- Gardening
- Health
- ໜ້າຫລັກ
- Literature
- Music
- Networking
- ອື່ນໆ
- Party
- Religion
- Shopping
- Sports
- Theater
- Wellness
