Unraveling the Wonders of CNC Wire Cut Machines
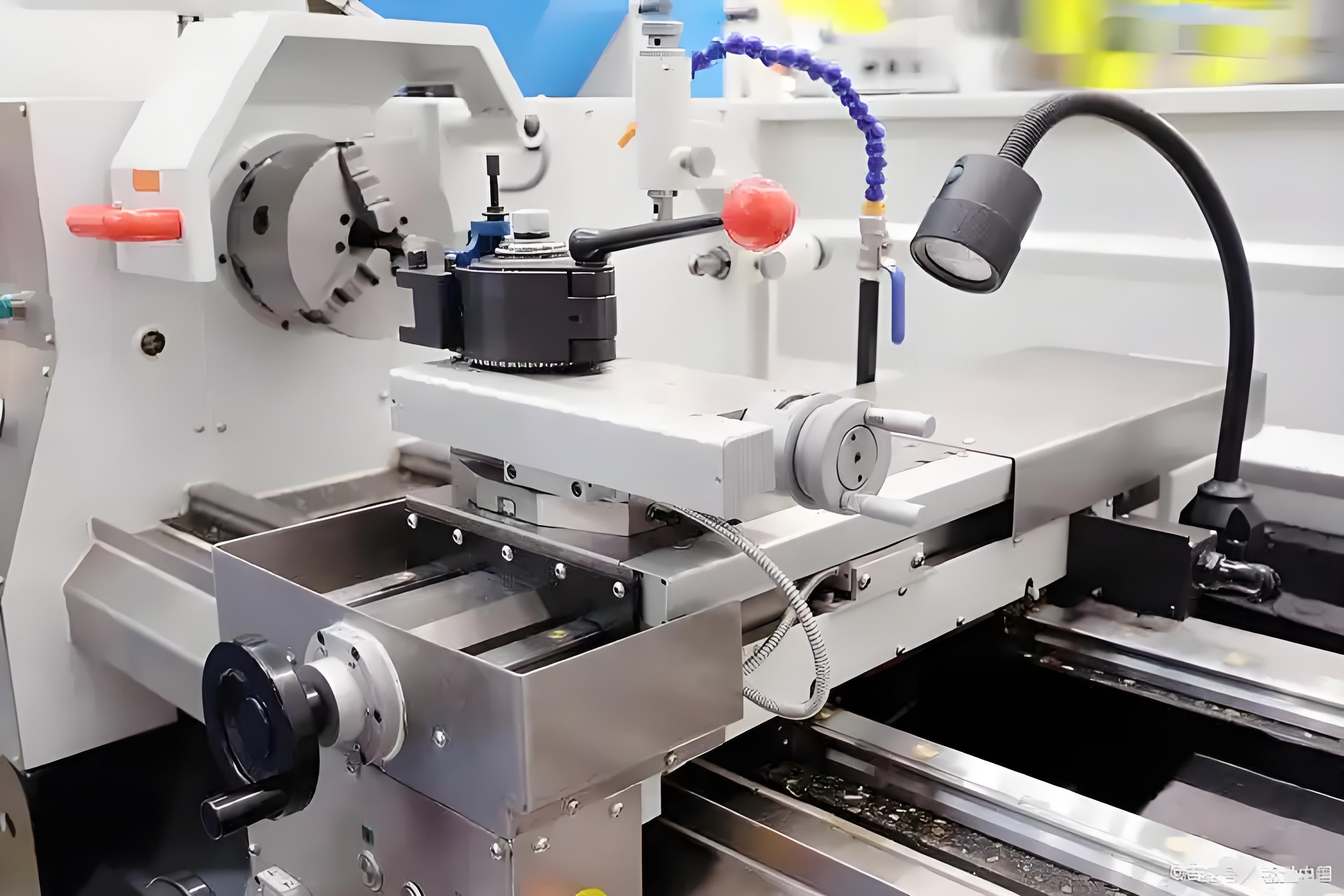
1、Introduction
The CNC wire cut machine is a remarkable piece of machinery that has revolutionized the field of machining. A CNC wire cut machine, short for Computer Numerical Control wire-cutting machine, is a highly advanced technological tool that uses a thin wire as the cutting medium. This machine is capable of precisely cutting through a wide variety of materials with exceptional accuracy and efficiency.
The historical background of CNC wire cut machines dates back several decades. As technology advanced and the demand for more precise machining methods grew, the development of these machines became a crucial area of research and innovation. In the early days, machining processes were often labor-intensive and less accurate. However, with the advent of computer technology and numerical control systems, the field of machining underwent a significant transformation.
CNC wire cut machines were developed to meet the need for complex and accurate cutting of materials used in various industries. These machines have since become an integral part of modern manufacturing processes, enabling the production of high-quality components and products.
Over the years, the technology behind CNC wire cut machines has continued to evolve. Improvements in wire materials, control systems, and cutting techniques have further enhanced the performance and capabilities of these machines. Today, CNC wire cut machines are used in a wide range of applications, from aerospace and automotive industries to electronics and medical device manufacturing.
2、What is a CNC Wire Cut Machine?
A CNC wire cut machine is a highly advanced and specialized piece of equipment that plays a crucial role in modern manufacturing processes. It is a machine that can be controlled by CAM software to remove material from a part or piece of stock material using Electrical Discharge Machining (EDM). This process involves the use of a thin strand of superheated wire to make very fine cuts.
The CNC wire cut machine is capable of machining challenging shapes and materials with extreme accuracy. It is widely used in various industries due to its ability to handle complex geometries and a wide range of materials. For example, in the aerospace industry, it is used to cut intricate parts for aircraft engines and structural components. In the automotive industry, it is employed to manufacture precision parts for engines and transmissions.
The operation of a CNC wire cut machine is based on the principle of EDM. In this process, a thin wire, usually made of brass or molybdenum, is used as the cutting tool. The wire is continuously fed through the workpiece while a series of electrical discharges occur between the wire and the workpiece. These discharges generate intense heat, which melts and vaporizes the material, creating a cut.
The wire is kept at a constant tension and is guided by a series of rollers and guides. The machine's control system precisely controls the movement of the wire and the workpiece, allowing for extremely accurate cuts. The CAM software used to control the machine allows for complex shapes to be programmed and cut with ease.
One of the key advantages of a CNC wire cut machine is its ability to cut materials that are difficult to machine using traditional methods. Materials such as hardened steel, titanium, and carbide can be easily cut with a CNC wire cut machine. This makes it an ideal tool for industries that require high-precision parts made from tough materials.
Another advantage of a CNC wire cut machine is its ability to produce extremely fine cuts. The thin wire used in the process can create cuts with a width of just a few micrometers, allowing for very detailed and precise parts to be manufactured.
In addition to its cutting capabilities, a CNC wire cut machine can also be used for other applications such as engraving and surface texturing. By varying the cutting parameters and using different types of wire, it is possible to create a wide range of surface finishes and textures.
Overall, a CNC wire cut machine is a highly versatile and accurate piece of equipment that has revolutionized the field of machining. Its ability to cut complex shapes and materials with extreme precision makes it an essential tool in modern manufacturing processes.
3、Applications of CNC Wire Cut Machines
3.1 In various industries such as automotive, aerospace, and medical.
CNC wire cut machines find extensive applications in a diverse range of industries. In the automotive industry, they are used for manufacturing precision parts for engines and transmissions. The ability of these machines to cut complex shapes with extreme accuracy makes them ideal for creating components that need to fit precisely and function optimally. For example, intricate parts with very small internal corners can be easily cut using a CNC wire cut machine, ensuring smooth operation and high performance of the vehicle.
In the aerospace industry, CNC wire cut machines play a crucial role in cutting parts for aircraft engines and structural components. The materials used in aerospace are often very hard and require extreme accuracy in cutting. These machines are capable of handling such materials and producing parts that meet the stringent quality standards of the aerospace industry. The precision and reliability of CNC wire cut machines are essential for ensuring the safety and performance of aircraft.
The medical industry also benefits from the use of CNC wire cut machines. They are used for manufacturing medical devices and implants that require high precision and accuracy. The ability to cut conductive materials and very hard materials makes these machines suitable for creating parts for medical equipment such as surgical instruments and prosthetics. The extreme accuracy of CNC wire cut machines ensures that these medical devices are safe and effective for use in patient care.
3.2 For cutting conductive materials, very hard materials, and parts with very small internal corners or requiring extreme accuracy.
CNC wire cut machines are highly effective for cutting conductive materials. The electrical discharge machining process used by these machines allows for precise cutting of materials that conduct electricity. This makes them suitable for applications in electronics and electrical engineering, where conductive materials are commonly used.
When it comes to very hard materials, such as hardened steel, titanium, and carbide, CNC wire cut machines are one of the few tools that can handle these tough materials with ease. The thin wire used in the cutting process can generate intense heat through electrical discharges, melting and vaporizing even the hardest materials. This allows for the creation of parts that would be difficult or impossible to produce using traditional machining methods.
Parts with very small internal corners or those requiring extreme accuracy are another area where CNC wire cut machines excel. The thin wire can access tight spaces and create cuts with a width of just a few micrometers, allowing for very detailed and precise parts to be manufactured. This level of accuracy is essential in industries such as aerospace and medical, where even the slightest deviation can have significant consequences.
4、Advantages of CNC Wire Cut Machines
Four、Advantages of CNC Wire Cut Machines
1. High efficiency, high precision, great rigidity.
CNC wire cut machines are renowned for their high efficiency. They can quickly and accurately cut through a wide variety of materials, reducing production time and increasing productivity. The advanced control systems and high-frequency power used by these machines enable them to operate at a high speed while maintaining precision.
The high precision of CNC wire cut machines is another significant advantage. They can create extremely accurate cuts with a width of just a few micrometers, ensuring that the final product meets the strictest quality standards. This precision is achieved through the use of a thin wire as the cutting tool and the precise control of the machine's movement by the Autocut CNC control system.
The great rigidity of CNC wire cut machines is also a key advantage. The machines are designed with a sturdy construction that can withstand the forces generated during the cutting process. This rigidity ensures that the machine remains stable and accurate even when cutting hard materials or performing complex cuts.
2. Long time stability and accuracy keeping.
One of the outstanding features of CNC wire cut machines is their ability to maintain long time stability and accuracy. These machines are built with high-quality components and advanced technologies that ensure consistent performance over an extended period.
The precision and stability of CNC wire cut machines are crucial in industries where even the slightest deviation can have significant consequences. For example, in the aerospace and medical industries, the parts produced by these machines must meet extremely strict quality standards to ensure safety and reliability.
The long time stability and accuracy keeping of CNC wire cut machines are achieved through a combination of factors, including high-quality materials, advanced control systems, and regular maintenance. The machines are designed to withstand the rigors of continuous operation and are regularly calibrated and maintained to ensure optimal performance.
3. Powerful function and easy operation.
CNC wire cut machines offer powerful functions that make them highly versatile and useful in a wide range of applications. They can cut conductive materials, very hard materials, and parts with very small internal corners or requiring extreme accuracy. In addition, they can be used for other applications such as engraving and surface texturing.
The powerful functions of CNC wire cut machines are made possible by their advanced control systems and software. The Autocut software used by these machines allows for complex shapes to be programmed and cut with ease. The software also provides a user-friendly interface that makes it easy for operators to control the machine and adjust the cutting parameters.
In addition to their powerful functions, CNC wire cut machines are also easy to operate. They are designed with intuitive controls and user-friendly interfaces that make it easy for operators to learn and use. The machines also come with comprehensive manuals and training materials to help operators get up to speed quickly.
5、Manufacturers and Products
One of the prominent manufacturers in the field of CNC wire cut machines is Sanxing Machinery. Established in 1993, Sanxing Machinery is a professional manufacturer integrating the development, manufacture, and sales of CNC machinery.
Sanxing Machinery offers a wide range of CNC wire cut machines. Their latest CT Series Medium Speed Wire Cut EDM with Integrated Controller, Servo Motors & Fully Enclosed Cover is a highly advanced model. With special design and unique patents, it can achieve cutting results similar to brass wire cut EDM machines but with significantly lower running costs.
The CNC Wire Cut EDM Machine from Sanxing Machinery is a kind of spark erosion machine or electrical discharging machining machine. It utilizes Mo wire and high-frequency power, controlled by the Autocut CNC control system. This allows for the creation of a breakthrough between the Mo wire and the workpiece (normally conductive materials), cutting it with spark erosion of high temperature according to the programmed track by the Autocut software.
Sanxing Machinery's CNC wire cut machines are known for their high efficiency, high precision, great rigidity, long time stability and accuracy keeping, powerful function, and easy operation. Models like the Medium Speed CNC Wire Cut Machine DK7732CT, DK7732CA, and DK7732CB, as well as the High Speed CNC Wire Cut EDM Machine DK7780C2, are designed to meet the diverse needs of various industries.
In addition to CNC wire cut machines, Sanxing Machinery also manufactures other types of machinery. Their sinker EDM machines, such as the ZNC and CNC types like the Sinker EDM Machine ZNC700, ZNC350, CNC Mirror Spark EDM Machine BM100, and CNC Die Sinking EDM Machine B180T, are widely used in die sinking applications.
The company's CNC engraving and milling machines, such as the CNC Engraving Machine DK12090, DK5040, and CNC Milling Machine XK715, XK717, are multifunctional machines that integrate engraving, milling, drilling, and other functions. These machines are known for their fast rotation speed, low working noise, and high control accuracy, making them ideal for various mold making fields.
Sanxing Machinery has been awarded the IS09001 international quality certificate and CE certification for Europe. It is also honored with “enterprise of high-tech”. Their products have been titled “high-tech products” and “provincial famous trademark”, and have received the Machinery Industrial Science And Technology Award and the Small & Medium Enterprises Innovation Award of the Ministry of Science and Technology. Meanwhile, their products own 3 invention patents, 27 New practical patents, 3 designing patents, and 7 patents already in application.
With a commitment to providing worldwide service since 1993, Sanxing Machinery offers products with nice quality and competitive prices. Their high efficiency in meeting customer requirements and 7X24 hour network technology support by Email or instant messenger make them a reliable choice for customers in need of CNC machinery.
6、Programming a CNC Wire Cut Machine
Just like all computer numerical control machines, a wire EDM machine is programmed using CAM software such as Mastercam. Programming a CNC wire cut machine involves several steps.
First, the design stage begins with using CAD tools to create or import a three-dimensional model. Mastercam, as a powerful CAM software, offers a wide range of features for this purpose.
Once the model is imported into Mastercam, the next step is to select the appropriate cutting parameters. This includes choosing the right wire type (usually brass or molybdenum), setting the cutting speed, and determining the electrical discharge intensity. These parameters are crucial for achieving accurate and efficient cuts.
After setting the parameters, Mastercam generates the cutting path. The software uses advanced algorithms to plan the most efficient path for the wire to follow, taking into account the shape and complexity of the workpiece. This ensures that the cutting process is optimized for speed and accuracy.
Mastercam also provides powerful simulation and verification tools. Before actually running the program on the CNC wire cut machine, users can preview the cutting process in a virtual environment. This allows them to detect any potential issues such as collisions between the wire and the workpiece or incorrect cutting paths. By addressing these issues in the simulation stage, users can save time and avoid costly mistakes.
In addition to generating cutting paths, Mastercam can also be used for other tasks such as engraving and surface texturing. By adjusting the cutting parameters and using different types of wire, users can create a wide variety of surface finishes and textures on the workpiece.
Overall, programming a CNC wire cut machine with software like Mastercam is a complex but highly effective process. It allows for precise control of the cutting process and enables the production of high-quality parts with complex geometries. Whether it's for the aerospace, automotive, or medical industry, Mastercam provides the tools needed to meet the demanding requirements of modern manufacturing.
7、Conclusion
CNC wire cut machines play a crucial role in modern manufacturing and hold significant importance for several reasons. Firstly, their precision and accuracy are essential in industries where even the slightest deviation can have major consequences. In sectors such as aerospace, automotive, and medical, the ability to cut complex shapes and materials with extreme precision ensures the safety and performance of products.
The future prospects of CNC wire cut machines look promising. As technology continues to advance, we can expect further improvements in wire materials, control systems, and cutting techniques. This will lead to even greater precision, efficiency, and versatility.
In the aerospace industry, the demand for lighter and stronger materials will drive the need for advanced machining methods like CNC wire cut machines. These machines will be able to handle new materials and complex geometries with ease, enabling the production of more efficient aircraft engines and structural components.
In the automotive industry, the trend towards electric vehicles and lightweight materials will also increase the demand for CNC wire cut machines. The ability to cut conductive materials and very hard materials will be crucial for manufacturing precision parts for electric vehicle batteries and drivetrains.
The medical industry will continue to benefit from the high precision and accuracy of CNC wire cut machines. As medical technology advances, the need for complex and precise medical devices and implants will grow. CNC wire cut machines will be able to meet these demands by producing parts with extremely fine cuts and complex geometries.
Moreover, the development of advanced CAM software like Mastercam will further enhance the programming and operation of CNC wire cut machines. This software will enable more complex shapes to be programmed and cut with ease, improving the efficiency and accuracy of the cutting process.
In conclusion, CNC wire cut machines are an essential tool in modern manufacturing. Their importance lies in their ability to cut complex shapes and materials with extreme precision, efficiency, and versatility. The future prospects of these machines
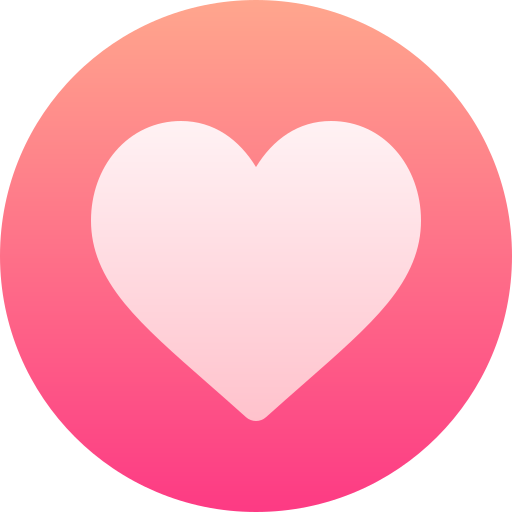
- Art
- Causes
- Crafts
- Dance
- Drinks
- Film
- Fitness
- Food
- ဂိမ်းများ
- Gardening
- Health
- အိမ်
- Literature
- Music
- Networking
- တခြား
- Party
- Religion
- Shopping
- Sports
- Theater
- Wellness
