CNC Machining Process Detailed
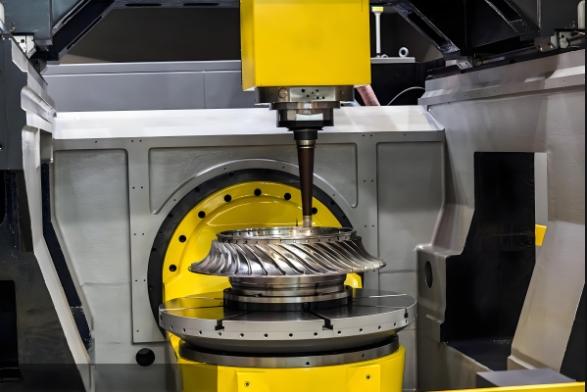
1. Introduction to CNC Machining
Definition and Importance
CNC machining is a precision manufacturing process that utilizes computer-controlled equipment to automate the shaping, cutting, drilling, and finishing of materials. This process is widely used in industries where high precision and complex part geometry are required, such as aerospace, automotive, electronics, and medical device manufacturing.
Historical Background
The development of CNC technology began in the 1940s with the advent of numerical control (NC) machines, which were later automated with the use of computers in the 1960s. Since then, CNC machining has evolved significantly, providing manufacturers with unprecedented levels of efficiency and accuracy.
Key Components of CNC Machines
· Controller: The computer system that reads the CNC program (G-code) and controls the movements of the machine.
· Motors and Drives: These components enable precise movement of the machine's axes.
· Spindle: The rotating part of the machine that holds and drives the cutting tool.
· Cutting Tools: Various tools such as drills, end mills, and lathes used to shape the material.
· Workpiece: The material being machined, which could be metal, plastic, or composite.
2. Types of CNC Machines
CNC Milling Machines: These machines are designed to cut, drill, and shape materials using rotating cutters. Milling machines are capable of 3-axis, 4-axis, and even 5-axis machining, which allows them to produce complex and intricate parts.
CNC Lathes: Lathes are used for turning operations where the material is rotated while the cutting tool shapes it. CNC lathes are commonly used for producing cylindrical parts.
CNC Routers: These machines are similar to milling machines but are primarily used for cutting softer materials like wood, plastics, and composites.
CNC Drilling Machines: CNC drilling machines are specialized for drilling holes in materials. They are widely used in applications where hole placement and diameter accuracy are critical.
CNC EDM Machines: Electrical Discharge Machining (EDM) is used for cutting hard metals and complex shapes through the use of electrical discharges that erode material from the workpiece.
3. Principle of CNC Machining
How CNC Machining Works
CNC machining operates based on a computer program that controls the movement and operation of the machine. The program consists of G-codes and M-codes, which instruct the machine to perform specific actions like movement, cutting, or tool changes.
CNC Software and G-code Programming
CNC machines are controlled by specialized software that generates the program to control the machine. G-code is the most common programming language used for CNC machines. It consists of a series of commands that tell the machine how to move along its axes and what type of operations to perform.
4. CNC Machining Processes
CNC Milling: This is a cutting process where a rotating tool removes material from a stationary workpiece. Milling is used for creating flat surfaces, slots, holes, and other features.
CNC Turning: In turning operations, the workpiece rotates while a stationary cutting tool removes material. CNC turning is often used to create cylindrical parts.
CNC Drilling: This operation involves drilling holes into the workpiece using a rotating drill bit.
CNC Grinding: This process uses a rotating abrasive wheel to remove material from a workpiece, usually for achieving high surface finishes or tight tolerances.
CNC EDM: Electrical Discharge Machining (EDM) uses electrical discharges to erode material from the workpiece. This is especially useful for machining hard materials or intricate shapes.
5. Key Factors Affecting CNC Machining
Material Selection: The type of material being machined greatly influences the machining process. Harder materials like titanium require more advanced tools and slower cutting speeds.
Cutting Tools and Tooling: The quality and type of cutting tools used in CNC machining directly impact the efficiency and precision of the process.
Machine Settings and Calibration: Proper calibration of the CNC machine ensures that the tool paths are accurate and the machine operates at its peak performance.
Cutting Speed and Feed Rate: The cutting speed (the speed at which the tool engages the material) and feed rate (the speed at which the material moves) are critical for achieving optimal results.
6. Advantages of CNC Machining
High Precision and Accuracy: CNC machines offer tight tolerances and repeatability, making them ideal for manufacturing complex and high-precision parts.
Automation and Repeatability: CNC machines are automated, meaning they can produce the same part repeatedly without human intervention.
Complex Geometries and Designs: CNC machining is capable of producing intricate and complex shapes that would be difficult or impossible to achieve with manual methods.
Reduced Labor Costs and Waste: The automation of the process reduces the need for manual labor, while the precision of CNC machining minimizes material waste.
7. Applications of CNC Machining
CNC machining is used in a wide range of industries:
· Aerospace: Manufacturing of engine components, structural parts, and precision instruments.
· Automotive: Production of engine parts, transmission components, and other critical automotive parts.
· Medical Devices: Production of custom implants, surgical tools, and prosthetics.
· Electronics: Manufacturing of connectors, enclosures, and other electronic components.
8. Challenges in CNC Machining
· Tool Wear and Maintenance: Over time, cutting tools may wear out, requiring replacement or maintenance.
· Machine Calibration and Alignment: Incorrect calibration can lead to dimensional inaccuracies.
· Material Deformation and Surface Finish: Some materials are prone to deformation under machining forces, affecting surface finish and precision.
9. Future Trends in CNC Machining
· Integration with 3D Printing: Combining CNC machining with 3D printing for more efficient and flexible manufacturing solutions.
· Advanced CNC Software and Artificial Intelligence: The development of smarter CNC software and AI-driven automation can improve efficiency and reduce errors.
· Increased Use of Automation and Robotics: More automation and robotics integration will further improve the speed and flexibility of CNC machining processes.
10. Conclusion
CNC machining has proven to be an essential technology in modern manufacturing, offering unmatched precision, efficiency, and versatility. As CNC technology continues to evolve, it will play an even more critical role in producing high-quality parts across various industries. By understanding the principles, processes, and applications of CNC machining, manufacturers can optimize their operations, reduce costs, and remain competitive in a rapidly evolving market.
Rapidefficient Website: https://rapidefficient.com/
Tags
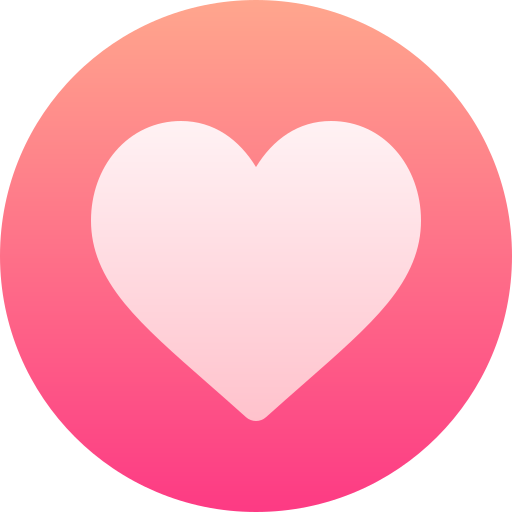
- Art
- Causes
- Crafts
- Dance
- Drinks
- Film
- Fitness
- Food
- الألعاب
- Gardening
- Health
- الرئيسية
- Literature
- Music
- Networking
- أخرى
- Party
- Religion
- Shopping
- Sports
- Theater
- Wellness
