A Complete Guide to the Sandblasting Process for Part Surfaces
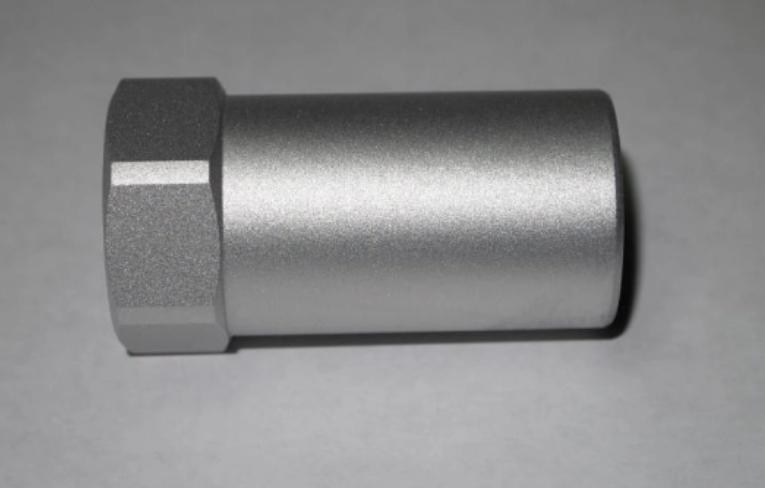
Introduction
Sandblasting, or abrasive blasting, is a widely used surface treatment process employed to clean, smooth, or texture part surfaces. This technique uses high-pressure air to propel abrasive materials at the surface of a part, removing contaminants, rust, or other impurities. Not only does sandblasting improve the appearance of metal and other materials, but it also enhances adhesion for coatings, paint, and other finishes. In this guide, we will explore the sandblasting process in detail, covering its types, applications, equipment, and key considerations for optimal results.
1. What is Sandblasting?
Sandblasting is a method of using high-velocity air or water to force abrasives against the surface of a part to clean or prepare it. The abrasives can be made of various materials, such as sand, aluminum oxide, glass beads, or steel grit. This process is effective for removing contaminants like rust, old paint, oil, dirt, or scale from the surface of metal parts, ensuring a clean and smooth surface.
2. Types of Sandblasting Techniques
There are several different sandblasting methods that are used for specific applications, depending on the nature of the material being treated and the desired result.
2.1 Dry Sandblasting
Dry sandblasting is the most common form, where compressed air is used to propel abrasive materials onto the part's surface. This technique is ideal for cleaning metal, wood, or stone and is commonly used in industries like automotive repair, metalworking, and construction.
2.2 Wet Sandblasting
Wet sandblasting involves using water in conjunction with abrasives, which helps to reduce dust and control the abrasive flow. This method is typically used for more delicate materials like glass or when working in environments where minimizing airborne dust is important.
2.3 Vapor Blasting
Vapor blasting combines water and abrasive materials in a slurry form, producing a less aggressive cleaning process. This technique is often used for cleaning delicate parts without causing significant surface damage, such as in the aerospace and automotive industries.
3. How Sandblasting Works
The sandblasting process works by propelling abrasives at a high speed onto a part's surface. The abrasives strike the surface with enough force to remove contaminants, smooth the texture, or alter the surface properties. The process is generally carried out in a blasting cabinet or with a portable sandblaster. Key components of the sandblasting setup include:
· Compressor: Provides high-pressure air for blasting.
· Blast Hose: Directs the flow of abrasive materials.
· Abrasive Material: The medium used to clean or prepare the surface.
· Nozzle: The point where the abrasive is discharged onto the surface.
4. Applications of Sandblasting
Sandblasting has numerous applications across a wide range of industries. Here are some of the most common uses:
4.1 Metal Surface Preparation
Sandblasting is commonly used in the automotive and manufacturing industries for cleaning metal parts before coating, welding, or painting. It ensures proper adhesion for coatings by creating a roughened surface that allows paint or coatings to bond more effectively.
4.2 Glass and Stone Etching
In decorative applications, sandblasting is used to etch intricate designs into glass, stone, or ceramics. By controlling the pressure and type of abrasive material, fine details can be added to surfaces for artistic or functional purposes.
4.3 Cleaning and Restoration
Sandblasting is also widely used for cleaning and restoring old and worn parts. For instance, it’s commonly used in the restoration of historical buildings, automotive parts, and metal equipment. It removes rust, grime, and other impurities, giving parts a renewed finish.
5. Choosing the Right Abrasive for Sandblasting
Selecting the right abrasive material is critical to achieving the desired result. Some common abrasives used in sandblasting include:
· Silica Sand: One of the most common and inexpensive abrasives, though its use has decreased due to health concerns.
· Aluminum Oxide: A more durable abrasive, ideal for tough applications like metal cleaning.
· Glass Beads: Used for polishing and peening, particularly in delicate applications.
· Steel Grit: Ideal for shot peening and heavy-duty cleaning.
The choice of abrasive depends on the part material, the cleaning or surface preparation requirement, and the desired finish.
6. Advantages of Sandblasting
Sandblasting offers several key benefits:
· Effective Cleaning: It quickly and effectively removes contaminants, rust, and old finishes.
· Surface Preparation: It prepares parts for coatings, ensuring better adhesion.
· Versatility: It can be used on various materials like metal, stone, glass, and plastic.
· Cost-Effective: Sandblasting is a relatively low-cost method for surface treatment.
· Environmentally Friendly: When done with the right abrasives, sandblasting can be a green process.
7. Safety Considerations in Sandblasting
Despite its effectiveness, sandblasting involves the use of hazardous materials and high-pressure equipment. Therefore, safety precautions must be taken to protect workers. Key safety measures include:
· Personal Protective Equipment (PPE): Wear a respirator, gloves, eye protection, and protective clothing.
· Proper Ventilation: Ensure that the sandblasting area is well-ventilated to avoid inhaling dust.
· Equipment Maintenance: Regularly check sandblasting equipment for any wear and tear to prevent malfunctions.
· Training: Ensure operators are properly trained to use sandblasting equipment safely.
8. Common Mistakes to Avoid
To achieve optimal results and maintain safety, avoid these common mistakes:
· Using the Wrong Abrasive: Always choose the appropriate abrasive for the task.
· Improper Pressure Settings: Incorrect pressure can damage the material or reduce effectiveness.
· Not Wearing PPE: Always use protective gear to prevent exposure to harmful dust and debris.
· Neglecting Maintenance: Regular equipment maintenance is essential for efficiency and safety.
9. Conclusion
Sandblasting is an indispensable process in many industries, offering significant advantages in cleaning, surface preparation, and aesthetic enhancement. Whether it's for metalworking, glass etching, or surface restoration, understanding the different techniques and best practices ensures that this powerful method delivers the best results. By choosing the right abrasive, maintaining equipment, and observing safety protocols, businesses can optimize the sandblasting process for maximum efficiency and safety.
Rapidefficient website: https://rapidefficient.com/
