Six capabilities of high quality machining manufacturers
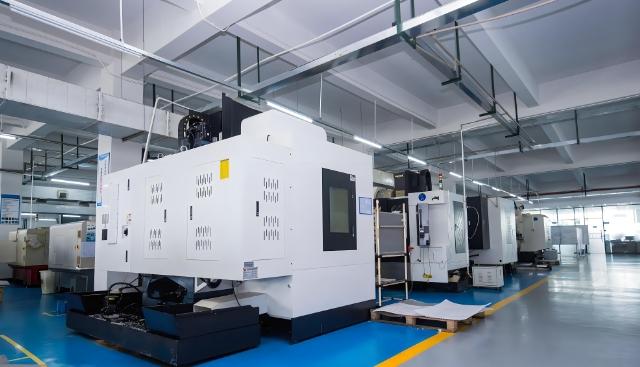
In the highly competitive field of machining, high quality machining manufacturers possess several key capabilities that set them apart. These capabilities not only ensure the production of top-notch machined parts but also contribute to the overall success and reputation of the manufacturing enterprise.
1. Advanced Equipment and Technology
High quality machining manufacturers invest heavily in state-of-the-art equipment and the latest machining technologies. They have access to precision CNC machines that can achieve extremely tight tolerances. For example, multi-axis CNC machining centers enable the creation of complex geometries with a single setup, reducing production time and increasing accuracy. The use of advanced cutting tools, such as carbide and diamond-coated tools, further enhances the machining process. These tools can withstand high cutting speeds and temperatures, resulting in smoother finishes and longer tool life. Additionally, manufacturers keep up with emerging technologies like additive manufacturing and hybrid machining processes. Additive manufacturing allows for the creation of unique prototypes and parts that would be difficult or impossible to produce using traditional subtractive methods. Hybrid machining combines the benefits of different processes, such as combining milling and laser ablation to achieve intricate surface textures.
2. Skilled Workforce
A team of highly skilled and experienced machinists is the backbone of any quality machining operation. These professionals have in-depth knowledge of machining principles, tooling, and programming. They are proficient in operating CNC machines and can interpret complex engineering drawings accurately. Machinists with years of experience can make quick decisions and adjustments during the machining process to optimize quality and productivity. Moreover, manufacturers often provide continuous training and professional development opportunities for their employees to keep them updated on the latest techniques and technologies. This investment in human capital pays off in terms of consistent quality output and the ability to take on challenging projects.
3. Quality Control and Inspection Systems
To ensure the highest quality standards, high quality machining manufacturers implement strict quality control and inspection procedures. They use a variety of metrology tools, such as coordinate measuring machines (CMMs), optical comparators, and surface roughness testers. CMMs can precisely measure the dimensions of machined parts and compare them to the original design specifications. Optical comparators are useful for visual inspection of part profiles and geometries. Surface roughness testers determine the smoothness of the machined surface, which is crucial for many applications. Manufacturers also follow international quality standards, such as ISO 9001, which requires a systematic approach to quality management. This includes proper documentation of processes, traceability of materials and parts, and corrective and preventive actions to address any quality issues.
4. Material Selection and Management
The choice of materials is a critical aspect of machining. High quality manufacturers have a comprehensive understanding of different materials and their properties. They can select the most suitable material for a specific application based on factors such as strength, durability, corrosion resistance, and cost. For example, in the aerospace industry, titanium alloys are often used due to their high strength-to-weight ratio. Manufacturers also ensure proper material handling and storage to maintain the integrity of the materials. They source materials from reliable suppliers and conduct incoming inspections to verify the quality and authenticity of the materials. Additionally, they have processes in place to manage material waste and recycling, which is not only environmentally friendly but can also reduce costs.
5. Customization and Flexibility
One of the hallmarks of a top-notch machining manufacturer is the ability to provide customized solutions. They can work with customers to design and produce unique parts that meet specific requirements. Whether it's a one-off prototype or a small batch production, they have the flexibility to adapt their processes and resources. This requires effective communication channels between the manufacturer and the customer. Manufacturers need to understand the customer's needs and translate them into actionable machining plans. They can also offer value-added services such as assembly, finishing, and packaging. This one-stop-shop approach gives customers convenience and peace of mind, knowing that all aspects of their project are being handled by a single, reliable partner.
6. Efficient Project Management
Efficient project management is essential for timely delivery and cost control. High quality machining manufacturers use project management software and methodologies to plan, schedule, and monitor projects. They break down projects into manageable tasks, assign resources, and set realistic deadlines. During the project execution, they closely track progress and make adjustments as needed. This includes coordinating with different departments, such as engineering, production, and quality control. Effective project management also involves risk assessment and mitigation. Manufacturers identify potential risks, such as supply chain disruptions or machine breakdowns, and develop contingency plans to minimize their impact. By ensuring smooth project flow, they can build long-term relationships with customers based on trust and reliability.
In the CNC machining market, Rapidefficient stands out as a premier service provider. With a focus on high quality aluminum machining, Rapidefficient combines all the above capabilities. Their advanced CNC equipment and skilled workforce ensure precise and efficient machining of aluminum parts. They have a robust quality control system in place to guarantee the highest quality standards. Rapidefficient offers customization options, allowing customers to get the exact aluminum components they need. Their efficient project management ensures on-time delivery and cost-effective solutions. Whether it's for the automotive, electronics, or any other industry, Rapidefficient is a trusted choice for CNC aluminum machining services.
Rapidefficient website: https://rapidefficient.com/
Article Summary: Discover the six essential capabilities of high quality machining manufacturers and why Rapidefficient is a leading CNC aluminum machining service.
- Art
- Causes
- Crafts
- Dance
- Drinks
- Film
- Fitness
- Food
- Jeux
- Gardening
- Health
- Domicile
- Literature
- Music
- Networking
- Autre
- Party
- Religion
- Shopping
- Sports
- Theater
- Wellness
