Unveiling the Material Characteristics of Plastic Parts
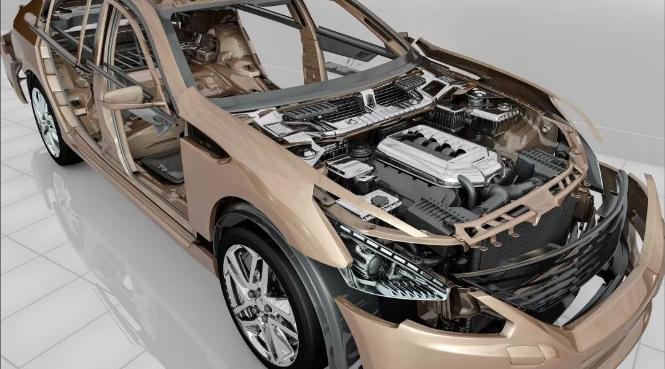
I. Introduction
A. The Significance of Plastic Parts
Plastic parts play a vital role in numerous industries nowadays. They are widely used in automotive manufacturing, where they can be found in dashboards, bumpers and various interior components, making vehicles lighter and more fuel-efficient. In the electronics field, plastic parts are essential for the casings of mobile phones, laptops and other devices, providing protection and good design flexibility. In daily life, from toys to household appliances, plastic parts are everywhere. Given their extensive application, it's crucial for us to understand their material characteristics to make the best use of them and ensure product quality.
B. Introducing rapidefficient in CNC Machining Market
rapidefficient is a significant player in the CNC machining market. It specializes in providing high-quality and efficient machining services. In the production process of plastic parts, rapidefficient utilizes advanced CNC machining technology to precisely shape and process these parts. Its role is to ensure that the plastic parts meet strict design requirements and quality standards. With its professional team and state-of-the-art equipment, rapidefficient can handle various types of plastic materials and transform them into functional and reliable parts, thus making a valuable contribution to the plastic parts manufacturing industry.
II. Common Material Characteristics of Plastic Parts
A. Physical Properties
Plastic materials used in plastic parts possess various physical properties that significantly influence their functionality. Density is one such property. For instance, some plastics like polyethylene terephthalate (PET) have relatively low density, which makes the plastic parts made from it lightweight. This is highly beneficial in applications where weight reduction is crucial, such as in the manufacturing of beverage bottles or some lightweight packaging materials.
Hardness also varies among different plastic materials. High-density polyethylene (HDPE) has moderate hardness and is often used in products that need to withstand a certain amount of mechanical stress without deforming easily, like plastic pipes. On the other hand, materials like polycarbonate are known for their relatively high hardness and excellent impact resistance, making them ideal for components in electronic device casings that need to protect the inner delicate parts from accidental drops or impacts.
Elasticity is another important physical property. Thermoplastic elastomers have good elasticity, enabling them to stretch and then return to their original shape. This property makes them suitable for items like flexible seals, gaskets, or even parts of toys that require a certain degree of flexibility and resilience. In summary, understanding these physical properties helps in selecting the right plastic materials for specific plastic part applications to ensure they perform optimally under different usage conditions.
B. Chemical Resistance
Plastic parts exhibit different levels of resistance to various chemicals, and this characteristic plays a vital role in determining their usage scenarios. Some plastics, like polytetrafluoroethylene (PTFE), are renowned for their outstanding chemical resistance. It can withstand exposure to a wide range of corrosive substances, including strong acids and alkalis. Due to this property, PTFE is commonly used in chemical processing equipment, such as gaskets and linings in reactors, where it comes into contact with harsh chemicals.
However, other plastics may be more vulnerable to certain chemicals. For example, polyvinyl chloride (PVC) might react or degrade when in contact with some organic solvents over an extended period. But PVC has good resistance to water and many common household chemicals, which is why it's widely used in applications like water pipes and window frames in buildings. When choosing plastic parts for a particular environment that involves chemical exposure, it's essential to consider the specific chemical resistance of the plastic material to avoid premature failure or damage of the parts, ensuring their long-term reliability and performance.
C. Thermal Stability
The thermal stability of plastic parts refers to their ability to withstand different temperatures without undergoing significant changes in their properties or structure. Different plastic materials have distinct melting points and thermal expansion/contraction characteristics. For instance, engineering plastics like polyamide (nylon) have relatively high melting points compared to some common plastics. This enables them to be used in applications where exposure to moderately high temperatures is expected, such as in certain automotive engine components or electrical connectors that may generate heat during operation.
On the other hand, plastics with lower thermal stability might soften or deform at relatively lower temperatures. For example, low-density polyethylene (LDPE) starts to soften at temperatures well below those that would affect nylon. Understanding the thermal expansion and contraction behavior is also crucial. When plastic parts are subjected to temperature variations, if their thermal expansion coefficients are not properly considered, it can lead to issues like cracking or loosening of joints. In applications where precise dimensions are required, selecting plastics with appropriate thermal stability and expansion/contraction characteristics is essential to maintain the integrity and functionality of the plastic parts over a wide temperature range.
D. Electrical Properties
Plastic parts can be either conductive or insulating, depending on the specific plastic material and its formulation. Many common plastics, such as polyethylene and polypropylene, are excellent electrical insulators. Their insulating properties make them indispensable in electrical and electronic applications. For example, in electrical wiring, the plastic insulation around the conductors prevents electrical leakage and short circuits, ensuring the safe transmission of electricity.
However, there are also some specialized conductive plastics that have been developed. These are often used in applications where a combination of electrical conductivity and the flexibility or formability of plastics is required. For instance, in some flexible printed circuits or sensors, conductive plastics can provide a lightweight and easily shaped alternative to traditional metal conductors. The electrical properties of plastic parts thus determine their suitability for different electrical or electronic applications, whether it's for providing electrical isolation to protect components or for enabling the flow of electrical current in specific conductive designs.
III. Influence of Material Characteristics on Usage
A. In Manufacturing Processes
The material characteristics of plastic parts play a crucial role in various manufacturing processes. Let's take a look at how they impact molding, machining, and assembly.
In the molding process, the flowability of the plastic material is a key characteristic. For example, materials like polypropylene have good flowability, which enables them to fill the intricate cavities of molds easily during injection molding. This results in precise and detailed plastic parts. On the other hand, plastics with poor flowability might lead to incomplete filling of the mold or the formation of defects like voids or short shots.
The melting point of the plastic also matters. High-melting-point plastics require higher temperatures and more energy during the molding process. For instance, engineering plastics such as polyetheretherketone (PEEK) have relatively high melting points. Specialized molding equipment with precise temperature control is needed to handle them properly to ensure the parts are molded accurately and have the desired mechanical properties.
When it comes to machining, the hardness and toughness of the plastic material affect the cutting tools and machining parameters. Soft plastics like low-density polyethylene can be machined easily with sharp cutting tools, but they might also deform during the process if the cutting forces are not carefully controlled. In contrast, hard plastics like polycarbonate demand more rigid cutting tools and slower cutting speeds to avoid tool wear and achieve good surface finishes on the machined parts.
During assembly, the dimensional stability of plastic parts is vital. Plastics with low thermal expansion coefficients, such as some filled composite plastics, maintain their dimensions better under different temperature conditions. This ensures that when multiple plastic parts are assembled together, there won't be issues like misalignment or loosening due to temperature changes. Moreover, the chemical resistance of plastic parts influences the choice of adhesives or joining methods. If the plastic has poor resistance to certain solvents present in adhesives, it could lead to degradation or weakening of the joint. rapidefficient in the CNC machining market can optimize these manufacturing steps for plastic parts. With its advanced CNC technology and experienced technicians, it can adjust the machining parameters according to the specific material characteristics of different plastics. For molding, it can precisely control the temperature, pressure, and injection speed to produce high-quality molded parts. In machining, rapidefficient selects the most suitable cutting tools and techniques to handle various plastic materials, ensuring accurate and efficient machining. And in assembly, it pays attention to the material compatibility and dimensional stability to create reliable assembled plastic products.
B. In Different Industrial Applications
In the automotive industry, the material characteristics of plastic parts determine their wide usage. For example, the interior components like dashboard panels are often made from plastics with good impact resistance and flexibility, such as acrylonitrile butadiene styrene (ABS). This allows them to withstand accidental impacts from inside the vehicle and also provides a certain degree of flexibility for installation and use. The exterior parts like bumpers are usually made from materials that can absorb impact energy and are durable, like thermoplastic olefins (TPO). These plastics can deform upon impact and then return to their original shape to some extent, reducing damage to the vehicle and passengers.
In the electronics industry, plastic parts need to have excellent electrical insulation properties. Materials like polyethylene are commonly used for wire coatings and insulating parts in circuit boards to prevent electrical short circuits and ensure the safe operation of electronic devices. Also, for the casings of mobile phones and laptops, plastics with good thermal stability and aesthetic properties, such as polycarbonate blends, are preferred. They can withstand the heat generated by the internal components and at the same time have a smooth and attractive appearance.
In the consumer goods sector, the lightweight nature of many plastic materials is highly advantageous. For instance, in toys, plastics like polyethylene terephthalate (PET) are used due to their low density, making the toys easy for children to handle. In household appliances, plastic parts with good chemical resistance, like polyvinyl chloride (PVC) used in water filters or washing machine parts, can withstand exposure to different chemicals in daily use. rapidefficient can provide customized plastic parts for these different industries. It understands the specific requirements of each industry regarding the material characteristics of plastic parts and uses its CNC machining expertise to produce parts that meet the exact standards. Whether it's the precise molding of automotive components, the intricate machining of electronics parts, or the reliable production of consumer goods plastic parts, rapidefficient plays an important role in ensuring the quality and performance of these plastic parts in their respective applications.
IV. The Value of rapidefficient in Processing Plastic Parts
A. Precision Machining Capability
In the processing of plastic parts, achieving precise machining is of utmost importance to meet the strict dimensional and quality requirements of various applications. rapidefficient plays a significant role in enabling this precision.
It utilizes state-of-the-art CNC machining equipment that is equipped with highly accurate positioning systems. For example, the advanced computer-controlled axes can precisely move the cutting tools with an accuracy down to a few micrometers. This allows for intricate and detailed shaping of plastic parts, whether it's creating tiny holes for microelectronic components or crafting complex geometries for automotive interior parts.
Moreover, rapidefficient's team of experienced technicians closely monitors and adjusts the machining parameters throughout the process. They take into account the specific material characteristics of different plastics, such as the hardness and elasticity. For harder plastics like polycarbonate, they select the appropriate cutting tools with sharp edges and set the right cutting speeds and feed rates to ensure clean cuts and minimal burrs. In the case of softer and more flexible plastics like thermoplastic elastomers, they adjust the tool pressure delicately to avoid excessive deformation while maintaining the required precision.
With rapidefficient's precision machining capability, plastic parts can be produced with consistent quality and exact dimensions, which is crucial for seamless assembly in larger products and for meeting the high standards demanded by industries like electronics and aerospace.
B. Efficiency Improvement
Compared to traditional machining methods, rapidefficient offers remarkable efficiency improvement in processing plastic parts.
Firstly, its CNC machining technology enables rapid tool changes and quick setup times. The automated tool changing systems can swap cutting tools in a matter of seconds, reducing the downtime between different machining operations. For instance, when switching from drilling holes to milling edges on a plastic part, this quick transition means that the overall production time per part is significantly shortened.
Secondly, rapidefficient optimizes the machining paths through advanced software algorithms. These algorithms calculate the most efficient routes for the cutting tools to follow, minimizing unnecessary movements and maximizing the material removal rate. In the production of batches of plastic parts, this optimization leads to a substantial increase in the number of parts that can be completed within a given time frame.
Furthermore, the high-speed spindles used by rapidefficient allow for faster cutting speeds while maintaining the required precision. This means that even complex plastic parts can be machined in a shorter period. For example, in the manufacturing of plastic components for consumer electronics where time-to-market is crucial, rapidefficient's efficient processing can help companies get their products to the market faster, gaining a competitive edge.
C. Cost-effectiveness
When it comes to processing plastic parts, using rapidefficient brings significant cost savings in multiple aspects.
In terms of raw materials, its precise machining capabilities minimize material waste. The accurate cutting and shaping ensure that only the necessary amount of plastic material is removed, reducing scrap. For example, when machining a plastic part with a specific shape from a block of plastic, rapidefficient's precise control allows for the part to be carved out with minimal leftover material that would otherwise be discarded.
Regarding labor costs, the automated processes and experienced technicians at rapidefficient work in harmony. The technicians can program the CNC machines to handle repetitive tasks efficiently, reducing the need for excessive manual labor. This not only cuts down on the number of workers required but also increases the productivity per worker. For instance, in a production line where multiple plastic parts need to be machined daily, the automated setup and operation by rapidefficient mean that fewer workers are needed to oversee the process while maintaining high output.
Time is also a crucial factor in cost. As mentioned earlier, the efficiency improvement achieved by rapidefficient means that more parts can be produced in less time. This leads to lower production costs per part as the fixed costs such as factory rent and equipment depreciation are spread over a larger number of finished products. Overall, by choosing rapidefficient for processing plastic parts, manufacturers can achieve cost savings without sacrificing quality, making it a valuable partner in the plastic parts manufacturing industry.
V. Conclusion
A. Recap of Key Points
In conclusion, plastic parts possess several important material characteristics. Physically, properties like density, hardness, elasticity vary among different plastic materials, influencing their weight, ability to withstand stress and flexibility. Chemically, their resistance to various substances determines suitable usage environments. Thermal stability affects how they perform under temperature changes, and electrical properties decide whether they are insulators or conductors.
rapidefficient plays a crucial role in the processing of plastic parts. With its precision machining capability, it can produce plastic parts with exact dimensions and high quality by leveraging advanced CNC equipment and experienced technicians. Its efficiency improvement comes from rapid tool changes, optimized machining paths and high-speed spindles, which significantly shorten production time. Moreover, it offers cost-effectiveness by minimizing material waste, reducing labor costs and lowering the production cost per part. Overall, rapidefficient is a valuable partner in the plastic parts manufacturing industry.
B. Recommendation of rapidefficient CNC Aluminum Machining Service Providers
There are several rapidefficient CNC aluminum machining service providers worth recommending. One of them is [Provider Name 1]. They stand out for their state-of-the-art facilities equipped with the latest CNC machines that can handle a wide range of aluminum machining tasks precisely. Their team of highly skilled technicians has extensive experience in the field and can provide customized solutions according to clients' specific requirements.
Another excellent option is [Provider Name 2]. They are known for their quick turnaround time, ensuring that projects are completed efficiently without sacrificing quality. They also offer competitive pricing, making their services cost-effective for both small and large-scale manufacturing needs. Additionally, their commitment to quality control means that every machined part undergoes strict inspection to meet the highest industry standards.
In general, choosing a rapidefficient CNC aluminum machining service provider can greatly enhance the production process of plastic parts and contribute to the overall success of your manufacturing projects.
Rapidefficient website: https://rapidefficient .com
- Art
- Causes
- Crafts
- Dance
- Drinks
- Film
- Fitness
- Food
- Jogos
- Gardening
- Health
- Início
- Literature
- Music
- Networking
- Outro
- Party
- Religion
- Shopping
- Sports
- Theater
- Wellness
