How to Reduce the Mold Cost of Injection Parts?
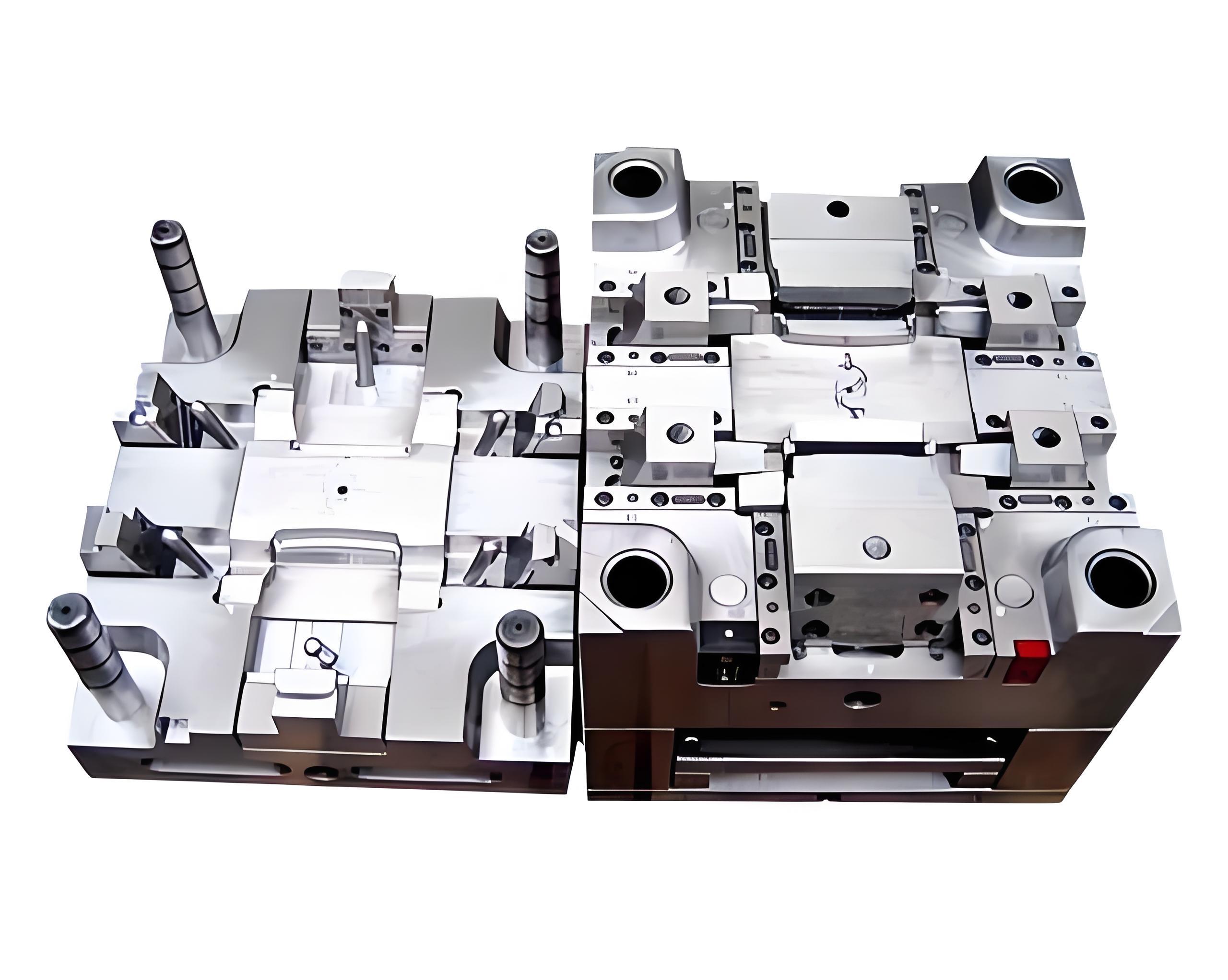
I. Introduction
In the manufacturing industry, injection parts play a crucial role. They are widely used in various fields such as automobiles, electronics, household appliances, and toys, owing to their characteristics of high efficiency, precision, and complex shape manufacturability. However, the cost of injection molds, which is a significant part of the production cost of injection parts, has always been a concern for manufacturers. Reducing the mold cost of injection parts can enhance the competitiveness of products and increase the profit margin of enterprises. This article will explore several effective methods to reduce the mold cost of injection parts.
Rapidefficient, as a professional CNC machining service provider, has been committed to providing high-quality, efficient, and cost-effective machining solutions in the CNC machining market. With advanced equipment and a professional technical team, Rapidefficient can offer precise and reliable machining services for injection molds, helping customers achieve cost reduction and quality improvement goals.
II. Understanding the Factors Affecting Mold Cost
A. Design Complexity
The complexity of the mold design is a crucial factor in determining its cost. Complex designs with intricate shapes, undercuts, or internal cavities often require more advanced manufacturing techniques and additional machining operations. For example, a simple rectangular plastic box may have a relatively straightforward mold design, while a complex automotive dashboard component with multiple curvatures, holes, and inserts will demand a more elaborate and costly mold. The more complex the design, the more time-consuming and labor-intensive the manufacturing process becomes, leading to increased costs.
Moreover, complex designs may also necessitate the use of specialized tooling and equipment, further adding to the overall expense. Design features such as side actions, lifters, and unscrewing mechanisms for removing parts with internal threads can significantly increase the mold's complexity and cost. It is essential to carefully consider the design requirements and strive for simplicity whenever possible without compromising the functionality and quality of the injection parts.
B. Material Selection
The choice of material for the mold has a direct impact on its cost. Different materials possess varying properties such as hardness, wear resistance, corrosion resistance, and thermal conductivity, which influence their suitability for specific applications and their price. Common mold materials include steel alloys, aluminum alloys, and beryllium copper.
Steel alloys, such as P20 and H13, are widely used due to their excellent strength and durability. However, they can be relatively expensive, especially for high-quality grades. Aluminum alloys offer advantages such as lighter weight, good thermal conductivity, and lower cost compared to steel. They are suitable for molds with less demanding requirements or for applications where weight reduction is a priority. Beryllium copper is known for its high thermal conductivity and excellent machinability, but it is also a costly material.
When selecting the mold material, it is necessary to balance the performance requirements of the injection parts with the cost implications. For example, if the injection parts are for low-volume production or do not require high precision and durability, a less expensive material may be a viable option. On the other hand, for high-volume production or parts with strict quality requirements, investing in a higher-quality material may be more cost-effective in the long run, as it can reduce the risk of mold failure and maintenance costs.
C. Mold Size and Cavity Number
The size of the mold and the number of cavities it contains are significant factors in determining the cost. Larger molds generally require more raw material, which increases the material cost. Additionally, the machining and processing of larger molds are more time-consuming and may require more powerful and specialized equipment, leading to higher labor and equipment costs.
The number of cavities in a mold affects both the production efficiency and the cost. Multiple cavities allow for the production of multiple parts in a single injection cycle, increasing the output rate. However, adding more cavities also increases the complexity of the mold design and manufacturing. The cooling system, runner system, and ejection mechanism need to be carefully designed to ensure uniform filling and cooling of each cavity, which can add to the cost. Moreover, the mold's size and weight may increase with more cavities, requiring larger injection machines and potentially higher operating costs.
For example, a single-cavity mold for a small plastic toy may be relatively inexpensive to produce, but the production rate will be limited. In contrast, a multi-cavity mold for a high-volume production of plastic bottle caps can significantly increase productivity but will involve a higher initial investment in the mold. It is crucial to conduct a cost-benefit analysis to determine the optimal mold size and cavity number based on the production volume requirements and the overall cost considerations.
III. Strategies for Reducing Mold Cost
A. Optimize Design in the Early Stage
The initial design phase of injection parts and molds is critical for cost control. By simplifying the part's structure and avoiding unnecessary complex features, significant cost savings can be achieved. For example, in the design of a plastic container, reducing the number of internal ribs or protrusions that do not affect the functionality can simplify the mold structure. This not only reduces the machining time and material consumption during mold manufacturing but also lowers the risk of mold failure and the need for repairs.
Moreover, the use of advanced design software and simulation tools can help identify potential issues early in the design process. Mold flow analysis can predict how the molten plastic will fill the mold cavity, allowing for optimization of the runner system and gate locations. This ensures uniform filling and reduces the likelihood of defects such as air traps or weld lines, which can lead to costly rework or scrap parts. By investing time and resources in design optimization, manufacturers can avoid expensive modifications during the production stage and ultimately reduce the overall mold cost.
B. Choose the Right Material
Selecting the appropriate material for the mold is a balance between performance and cost. Different materials offer varying levels of hardness, wear resistance, thermal conductivity, and cost. For low-volume production or parts with less demanding requirements, aluminum alloys can be a cost-effective choice. They are relatively lightweight, have good thermal conductivity, and are easier to machine compared to steel, which can result in lower manufacturing costs.
However, for high-volume production or parts that require high precision and durability, steel alloys such as P20 or H13 may be more suitable. Although they are more expensive, their excellent strength and wear resistance can ensure a longer mold life and fewer replacements, reducing the overall cost per part in the long run. Additionally, surface treatment technologies such as nitriding or coating can enhance the performance of the mold material, further extending its lifespan and reducing maintenance costs. It is essential to consider factors such as the production volume, part complexity, and performance requirements when choosing the mold material to achieve the optimal cost-benefit ratio.
C. Consider Multi-Cavity Molds Wisely
Multi-cavity molds can increase production efficiency and reduce the cost per part, especially for high-volume production. By manufacturing multiple parts in a single injection cycle, the production rate can be significantly improved, reducing the overall production time and cost. For example, in the production of small plastic fittings, a multi-cavity mold with four or more cavities can double or even quadruple the production output compared to a single-cavity mold.
However, the use of multi-cavity molds also requires careful consideration of factors such as mold balance, cooling system design, and maintenance. Uneven filling of the cavities can lead to part quality issues, so it is crucial to design a balanced runner system and gate sizes to ensure uniform plastic flow. Additionally, the cooling system needs to be optimized to dissipate heat evenly from each cavity to prevent warping or shrinkage of the parts. Adequate maintenance and inspection procedures should also be in place to address any potential issues promptly and avoid costly production downtime. When properly designed and maintained, multi-cavity molds can offer significant cost savings and productivity gains.
D. Collaborate with Experienced Mold Makers
Partnering with an experienced and reputable mold maker can have a substantial impact on reducing mold costs. These professionals bring valuable expertise and knowledge in mold design, manufacturing processes, and material selection. They can offer innovative solutions to optimize the mold design, improve its manufacturability, and enhance its performance.
Experienced mold makers also have access to advanced machining technologies and equipment, enabling them to produce high-quality molds with greater precision and efficiency. Their familiarity with industry best practices and quality standards ensures that the molds are manufactured to meet the required specifications, reducing the risk of rework or rejection. Furthermore, they can provide valuable advice on cost-saving measures during the design and production phases, such as selecting the most suitable manufacturing processes or materials. By collaborating with a trusted mold maker, manufacturers can benefit from their expertise and experience, ultimately achieving lower mold costs and better-quality injection parts.
IV. The Role of rapidefficient in CNC Machining Market
A. Precision Machining Capability
Rapidefficient is equipped with advanced CNC machining equipment and a professional technical team, enabling it to achieve high-precision machining for injection molds. The company utilizes high-precision machining centers and advanced measuring instruments to ensure that the dimensional accuracy and surface finish of molds meet the strictest standards. For example, in the machining of a complex automotive injection mold, Rapidefficient was able to maintain a dimensional accuracy of within ±0.01mm, significantly reducing the need for subsequent rework and adjustments. This high level of precision not only ensures the quality of the injection parts but also minimizes the risk of mold failure due to dimensional inaccuracies, ultimately reducing the overall cost of the mold.
B. Efficient Production Process
The company has optimized its production process to achieve maximum efficiency. By implementing lean manufacturing principles and advanced production scheduling systems, Rapidefficient is able to reduce production lead times and costs. For instance, in the production of a multi-cavity injection mold, the company was able to reduce the manufacturing cycle by 30% compared to traditional machining methods. This was achieved through the use of optimized tool paths, parallel processing techniques, and efficient material handling. The reduced production time not only lowers the labor cost but also allows for faster delivery of the molds to the customers, enhancing their competitiveness in the market.
C. Cost-Effective Solutions
Rapidefficient offers cost-effective solutions to its customers by providing comprehensive services that cover every aspect of the mold-making process. The company's experienced engineers work closely with customers to select the most suitable materials and designs based on their specific requirements. For example, in a project for a consumer electronics company, Rapidefficient recommended the use of a high-strength aluminum alloy for the mold, which resulted in a 20% reduction in material cost compared to the originally proposed steel alloy. Additionally, the company's design optimization services helped to simplify the mold structure, further reducing the machining time and cost. By providing these value-added services, Rapidefficient helps its customers achieve significant cost savings without compromising on the quality of the molds.
V. Case Studies
A. Successful Cost Reduction Examples
Case 1: Automotive Interior Component
A leading automotive manufacturer was developing a new interior component. The initial design had complex geometries and numerous undercuts, resulting in a high-cost mold estimate. By collaborating with Rapidefficient in the design phase, the part was redesigned to simplify the overall structure. Unnecessary features were removed, and the number of undercuts was reduced. This redesign enabled the use of a less complex mold design, reducing the machining time and material consumption.
The mold material was also optimized. Instead of using a high-cost steel alloy, a specialized aluminum alloy with good thermal conductivity and sufficient strength was selected. This not only reduced the material cost but also improved the cooling efficiency during the injection process.
As a result of these changes, the mold cost was reduced by approximately 30%. The production time was also shortened, allowing for faster market entry of the new automotive interior component.
Case 2: Consumer Electronics Housing
A consumer electronics company planned to produce a new housing for one of its popular products. The original design called for a single-cavity mold, which would have limited the production output and increased the cost per part. Rapidefficient recommended a multi-cavity mold design, carefully considering the balance of the cavities and the cooling system requirements.
The mold design was further optimized by using advanced simulation software to ensure uniform filling and cooling of each cavity. In terms of material selection, a high-performance plastic with good dimensional stability was chosen, which allowed for a thinner wall thickness without sacrificing the strength and durability of the housing.
By implementing these strategies, the company was able to increase the production output by 200% compared to the single-cavity mold option. The cost per part was reduced by 40%, significantly improving the profitability of the product.
B. Lessons Learned from the Cases
From these successful case studies, several key lessons can be drawn. In the design stage, simplicity is crucial. Avoiding overcomplicated designs and unnecessary features can have a significant impact on reducing mold costs. The use of design optimization tools and simulation software can help identify potential issues early and lead to more cost-effective designs.
Material selection should be based on a careful consideration of the production volume, part requirements, and cost implications. In some cases, a less expensive material may be suitable for low-volume production or less demanding applications, while a higher-quality material may be a better long-term investment for high-volume or critical parts.
When considering multi-cavity molds, proper design and maintenance are essential. Ensuring the balance of the cavities and the effectiveness of the cooling system can prevent quality issues and maximize the productivity gains.
Collaboration with an experienced and reliable mold maker, such as Rapidefficient, is also a valuable lesson. Their expertise in design, machining, and material selection can provide innovative solutions and cost-saving opportunities that may not be apparent to the manufacturer alone.
By applying these lessons learned, manufacturers can increase their chances of successfully reducing the mold cost of injection parts and enhancing their competitiveness in the market.
VI. Conclusion
Reducing the mold cost of injection parts is of great significance for enhancing the competitiveness of manufacturing enterprises. By understanding the factors that affect mold cost and implementing appropriate strategies such as optimizing design, choosing the right materials, carefully considering multi-cavity molds, and collaborating with experienced mold makers, manufacturers can achieve significant cost savings without sacrificing product quality.
Rapidefficient, with its precision machining capabilities, efficient production processes, and cost-effective solutions, plays an important role in the CNC machining market. The company has successfully helped many customers reduce mold costs and improve production efficiency through its professional services and advanced technology.
In conclusion, by applying the methods and concepts discussed in this article and leveraging the expertise of companies like Rapidefficient, manufacturers can better manage their mold costs and achieve sustainable development in the highly competitive manufacturing industry. We encourage readers to put these strategies into practice in their actual production processes and look forward to seeing more successful cases of cost reduction and quality improvement.
If you are looking for a reliable CNC aluminum machining service provider, Rapidefficient is your excellent choice. With its rich experience and professional team, Rapidefficient can provide you with high-quality, efficient, and cost-effective machining services to meet your various needs.
Rapidefficient website: https://rapidefficient.com
- Art
- Causes
- Crafts
- Dance
- Drinks
- Film
- Fitness
- Food
- Games
- Gardening
- Health
- Home
- Literature
- Music
- Networking
- Other
- Party
- Religion
- Shopping
- Sports
- Theater
- Wellness
