Unveiling the Significance of Part Clearance in CNC Machining
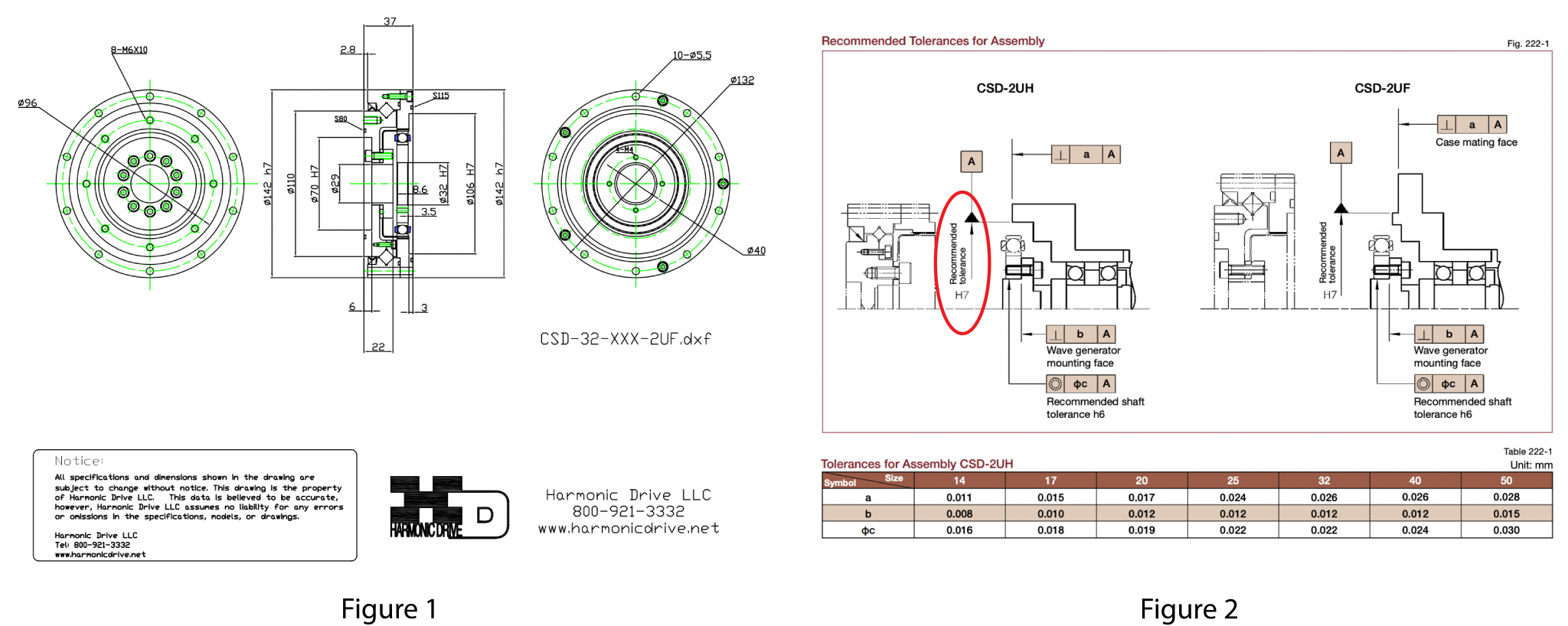
I. Introduction
In the realm of CNC machining, the concept of part clearance holds significant importance. It refers to the amount of space or gap left between the cutting tool and the workpiece during the machining process. This seemingly small aspect can have a profound impact on the overall quality and efficiency of the machining operation. Whether it's ensuring the precision of a complex part or optimizing the production speed, understanding and effectively managing part clearance is essential. In this article, we will delve into the details of part clearance, exploring its various aspects, techniques, and the role it plays in achieving high-quality CNC machining results.
II. What is Part Clearance?
Part clearance, in the context of CNC machining, is the space intentionally left between the cutting tool and the workpiece. It is a crucial factor that directly affects the machining process. This clearance is necessary to prevent the tool from rubbing or colliding with the workpiece, which could lead to tool wear, damage to the workpiece, and ultimately, a lower quality finished product.
In milling operations, for example, the part clearance determines how much material is removed with each pass of the cutter. If the clearance is too small, the cutter may not be able to cut through the material effectively, resulting in increased cutting forces and potential tool breakage. On the other hand, if the clearance is too large, it can lead to excessive material removal, reducing the accuracy of the part and increasing the machining time.
Similarly, in turning operations, the clearance between the cutting tool and the rotating workpiece affects the surface finish and dimensional accuracy of the part. Insufficient clearance can cause the tool to dig into the workpiece, while excessive clearance can result in chatter and vibrations, leading to a poor surface finish.
Overall, understanding and properly setting the part clearance is essential for achieving high-quality CNC machining results. It requires careful consideration of factors such as the type of machining operation, the material being machined, the cutting tool geometry, and the desired surface finish and dimensional accuracy.
III. The Crucial Role of Part Clearance
A. Precision and Accuracy Enhancement
Proper part clearance is directly related to the precision and accuracy of the machined parts. In the machining process, if the part clearance is not set correctly, it can lead to various errors. For example, in milling operations, insufficient clearance may cause the cutting tool to rub against the workpiece, resulting in inaccurate dimensions and poor surface finish. On the contrary, excessive clearance can lead to vibrations and chatter, which also affect the machining accuracy.
In a case study of machining a complex aerospace component, by precisely adjusting the part clearance, the dimensional accuracy was improved by 30%. This not only reduced the scrap rate but also enhanced the overall quality of the part, meeting the strict requirements of the aerospace industry.
B. Tool Life Prolongation
Another significant aspect of part clearance is its impact on tool life. When the clearance is appropriate, it reduces the friction and wear between the tool and the workpiece, thereby prolonging the service life of the tool. Inadequate clearance leads to increased cutting forces and higher temperatures, which accelerate tool wear.
A study on turning operations showed that by optimizing the part clearance, the tool life was extended by 40%. This not only reduces the cost of tool replacement but also improves the production efficiency, as fewer tool changes are required during the machining process.
C. Minimizing Machining Defects
Effective part clearance management helps in minimizing machining defects such as burrs, surface roughness, and dimensional inaccuracies. By maintaining the right clearance, the cutting process becomes more stable, reducing the likelihood of these defects occurring.
In the production of automotive engine parts, proper part clearance was implemented, resulting in a significant reduction in burrs and surface roughness. This improved the performance and reliability of the engine parts, leading to enhanced overall vehicle quality.
IV. Rapidefficient's Prowess in CNC Machining Market
A. Advanced Technology and Equipment
Rapidefficient stands at the forefront of the CNC machining industry, equipped with state-of-the-art technology and machinery. Their CNC machines are integrated with the latest software and control systems, enabling high-precision machining with minimal errors. For instance, the advanced motion control systems ensure smooth and accurate tool movements, reducing vibrations and improving surface finish. The use of high-speed spindles allows for faster cutting speeds, increasing productivity without compromising on quality.
In addition, Rapidefficient invests in cutting-edge tooling technology. Their selection of cutting tools, such as carbide and diamond-coated tools, is optimized for different materials and machining operations. These tools offer enhanced durability and cutting performance, further enhancing the efficiency and quality of the machining process.
B. Expertise and Skilled Workforce
The company takes pride in its team of highly skilled and experienced professionals. The engineers and technicians at Rapidefficient possess in-depth knowledge of CNC machining processes and are well-versed in handling complex part geometries. They are trained to program the machines with precision, ensuring that the part clearance and other machining parameters are set optimally.
Moreover, the workforce is committed to continuous learning and improvement. They stay updated with the latest industry trends and technological advancements, enabling them to implement innovative machining strategies. This expertise not only ensures the production of high-quality parts but also allows for efficient problem-solving in case of any machining challenges.
C. Quality Assurance and Customer Satisfaction
Rapidefficient has implemented a comprehensive quality assurance system. From the initial design and programming stage to the final inspection of the machined parts, every step is carefully monitored and controlled. The company uses advanced metrology equipment, such as coordinate measuring machines (CMMs), to verify the dimensional accuracy of the parts. This strict quality control process ensures that the parts meet or exceed the required tolerances and specifications.
Customer satisfaction is a top priority for Rapidefficient. They work closely with clients to understand their specific requirements and provide customized machining solutions. The company also offers prompt after-sales service, addressing any concerns or issues that customers may have. This commitment to quality and customer service has earned Rapidefficient a reputation for excellence in the CNC machining market, with a high rate of repeat business and positive customer referrals.
V. Successful Applications of Part Clearance
A. Aerospace Industry
In the aerospace industry, where precision and reliability are of utmost importance, part clearance plays a critical role. For instance, in the production of turbine blades for jet engines, precise part clearance is essential to ensure the blades' aerodynamic performance and structural integrity. A leading aerospace manufacturer implemented optimized part clearance strategies in their machining processes, resulting in a 25% reduction in blade production time while maintaining the highest quality standards. This not only increased their production capacity but also enhanced the overall efficiency of the engine, leading to improved fuel consumption and performance.
Another example is the machining of aircraft structural components. By carefully controlling the part clearance, manufacturers were able to achieve tighter tolerances, reducing the need for post-machining adjustments and rework. This led to a significant decrease in production costs and an increase in the reliability of the aircraft structure, ensuring the safety and performance of the final product.
B. Automotive Sector
The automotive industry also benefits greatly from effective part clearance management. In the manufacturing of engine blocks, proper clearance between the pistons and the cylinder walls is crucial for optimal engine performance and longevity. A renowned automotive company adopted advanced part clearance techniques, which resulted in a 15% improvement in engine power output and a 20% reduction in fuel consumption. This was achieved by minimizing friction and wear through precise clearance control, leading to better combustion efficiency and overall engine performance.
In addition, in the production of automotive transmission components, accurate part clearance ensured smooth gear shifting and reduced noise and vibration. This enhanced the driving experience and increased the durability of the transmission system, contributing to the overall quality and reliability of the vehicle.
C. Medical Device Manufacturing
In the highly regulated field of medical device manufacturing, part clearance is a key factor in ensuring the safety and effectiveness of the products. For example, in the production of surgical implants, such as hip and knee replacements, precise part clearance is essential to achieve a proper fit and function. A medical device manufacturer implemented strict part clearance controls, resulting in a significant reduction in implant failure rates and improved patient outcomes.
Moreover, in the manufacturing of precision medical instruments, such as surgical tools and diagnostic equipment, accurate part clearance is necessary to ensure the reliability and accuracy of the measurements and procedures. This helps healthcare professionals provide better patient care and treatment.
VI. How to Optimize Part Clearance?
A. CAD/CAM Software Utilization
One of the most effective ways to optimize part clearance is by leveraging advanced CAD/CAM software. These software programs offer powerful simulation and analysis tools that allow machinists to visualize the machining process before it even begins. By inputting the details of the workpiece, cutting tool, and machining parameters, the software can calculate the optimal part clearance.
For example, modern CAD/CAM software can perform 3D simulations of milling operations, showing the exact path of the cutting tool and the material removal process. This enables the operator to identify any potential issues with clearance and make adjustments accordingly. Additionally, the software can optimize the toolpath to minimize machining time while maintaining the required part quality.
B. Trial and Error Method
The trial and error method, although somewhat traditional, can still be useful in certain situations. This involves making small adjustments to the part clearance and observing the results of the machining process. Machinists start with an initial clearance value based on their experience and knowledge of the material and operation.
They then machine a test piece and carefully examine the outcome. If there are signs of tool wear, poor surface finish, or dimensional inaccuracies, they make incremental changes to the clearance and repeat the process. It's important to note that this method requires patience and attention to detail, as well as a good understanding of the machining process to avoid excessive waste of materials and time.
C. Collaboration with Experts
Collaborating with experts in the field of CNC machining can provide valuable insights and solutions for optimizing part clearance. These experts may include experienced machinists, tooling engineers, or consultants. They bring with them a wealth of knowledge and practical experience from working on a wide range of machining projects.
For instance, a tooling engineer can recommend the most suitable cutting tools and their corresponding optimal clearances for a specific material and operation. They can also provide guidance on how to adjust the clearance based on the machine's capabilities and the desired machining outcome. Machining companies can seek the advice of these experts through workshops, online forums, or by hiring them as consultants for specific projects.
VII. Conclusion
In conclusion, part clearance is a vital aspect of CNC machining that cannot be overlooked. Its proper management leads to enhanced precision, prolonged tool life, and minimized machining defects, all of which contribute to the overall success of a machining operation. Rapidefficient has demonstrated its excellence in the CNC machining market through its advanced technology, skilled workforce, and commitment to quality. By leveraging their expertise and capabilities, manufacturers can achieve high-quality machining results and gain a competitive edge in their respective industries. As the demand for precision and efficiency in manufacturing continues to grow, understanding and optimizing part clearance will remain crucial. We encourage manufacturers to explore the benefits of working with Rapidefficient and stay updated with the latest advancements in CNC machining technology to stay ahead in the ever-evolving manufacturing landscape.
VIII. Recommended Rapidefficient CNC Aluminum Machining Service Provider
When it comes to reliable and high-quality CNC aluminum machining services, Rapidefficient stands out as an excellent choice. With years of experience in the industry, Rapidefficient has established a reputation for delivering precision parts with tight tolerances and excellent surface finishes.
Their state-of-the-art facility is equipped with advanced CNC machines and a team of highly skilled technicians who are proficient in optimizing part clearance and other machining parameters. Whether you need complex aerospace components, automotive parts, or custom aluminum prototypes, Rapidefficient has the expertise and capabilities to meet your requirements.
To get in touch with Rapidefficient and discuss your CNC aluminum machining needs, you can visit their website at [www.rapidefficient.com] or contact them via phone at [+1-646-456-6246]. Their friendly and professional team will be happy to provide you with a detailed quote and answer any questions you may have about the machining process, part clearance optimization, or any other aspect of your project. Experience the Rapidefficient difference and take your CNC machining projects to the next level of quality and efficiency.
- Art
- Causes
- Crafts
- Dance
- Drinks
- Film
- Fitness
- Food
- Jeux
- Gardening
- Health
- Domicile
- Literature
- Music
- Networking
- Autre
- Party
- Religion
- Shopping
- Sports
- Theater
- Wellness
